|
 |
 |
 |

Технологическая схема |
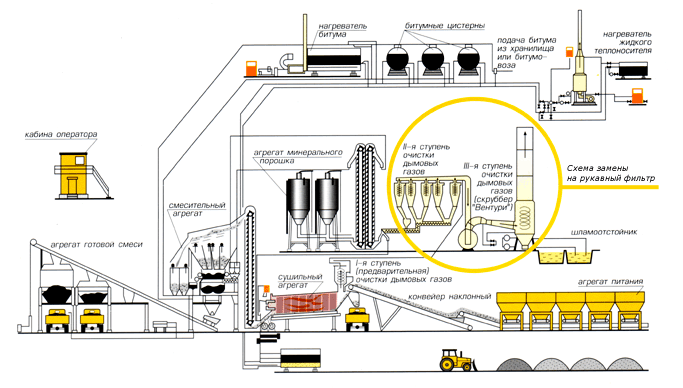 |
Установка рукавного фильтра |
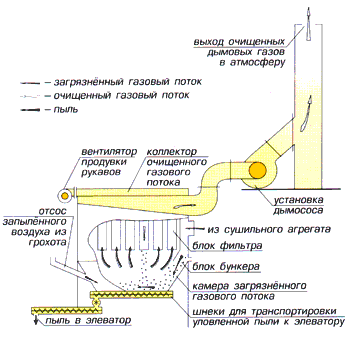 |
Конструкция асфальтосмесительных установок позволяет выполнять следующие операции технологического процесса:
- предварительное дозирование влажных каменных материалов в агрегате питания;
- просушивание и нагрев каменных материалов до рабочей температуры в сушильном барабане и подачу их к грохоту смесительного агрегата;
- сортировку нагретых каменных материалов на четыре фракции (0-5, 5-10, 10-20, 20-40 мм), временное хранение их в «горячем» бункере, дозирование и выдачу их в смеситель;
- трехступенчатую очистку выходящих из сушильного барабана дымовых газов от пыли в предварительной системе очистки, циклонах сухой пылеочистки и в мокром пылеуловителе скруббере «Вентури» (эффективность пылеулавливания составляет 99,7 99,85 % в зависимости от вида применяемых материалов) или очистку в рукавных фильтрах выбросы пыли составляют при этом не более 20 мг/м3;
- использование уловленной пыли путем подачи ее в отсек «пыли» бункера смесительного агрегата или на дозирование совместного с минеральным порошком;
- прием минерального порошка из автоцементовозов, дозирование и выдачу в смеситель;
- прием битума из битумовозов (или склада битума), временное хранение и нагрев его в битумных цистернах до рабочей температуры, дозирование и подачу в смеситель;
- выдачу смеси в автосамосвал или подачу ее скиповым подъемником в бункера готовой смеси;
- обогрев битумных коммуникаций и насосов горячим маслом, нагретым в змеевике нагревателя битума.
В установках обеспечено:
- автоматизированное и дистанционное весовое дозирование каменных материалов, битума, минерального порошка и пыли, их перемешивание, и выдача в бункер готовой смеси;
- контроль и регулирование температуры каменных материалов и отходящих дымовых газов на выходе из сушильного барабана, температуры топлива и готовой смеси;
- повторное использование воды (оборотное водоснабжение)для трубы «Вентури»;
- автоматическое или дистанционное управление всеми основными механизмами.
Управление всей установкой централизовано и осуществляется с пульта управления, размещенного в кабине оператора. Кабина оператора оборудована кондиционером и громкоговорящей связью. Блочный принцип изготовления повышает заводскую готовность узлов и позволяет значительно сократить сроки монтажа установки. Применение микропроцессорной системы управления обеспечивает у потребителя наиболее оптимальный, экономичный режим работы установки, повышает культуру производства и безотказность работы оборудования. При этом вся информация, в том числе и о возможных неисправностях, выводится на дисплей. Завод может поставлять изделия в комплектности, необходимой заказчику.
Технические характеристики
Основные параметры и технические характеристики |
Мобильность |
стационарная |
Производительность номинальная при влажности исходных материалов (песка и щебня) до 3%, т/ч |
160 |
Напряжение при трёхфазном переменном токе, В |
380 |
Частота тока, Гц |
50 |
Потребляемая мощность, кВт, не более |
420 |
Вместимость бункеров агрегата питания, шт. х м3 |
5 x 16 = 80 |
Высота загрузки в бункер, м |
3,4 |
Тип питателей |
объёмный, ленточный, регулируемый |
Ширина ленты конвейеров, мм |
650 |
Сушильный барабан, диаметр x длина, мм |
2200 x 8000 |
Привод сушильного барабана |
регулируемый, с плавным пуском и остановкой |
Вид топлива |
на выбор: жидкое или газообразное |
Количество фракций дозируемого каменного материала, шт. |
4 |
Погрешность взвешивания, % |
± 0,5 |
Вместимость бункера горячих каменных материалов, м3 |
17 |
Максимальная масса замеса, кг |
2200 |
Тип мешалки |
периодического действия |
Время приготовления одного замеса, сек. |
45...60 |
Общая вместимость бункеров агрегата готовой смеси, т (м3) |
100 (55,6) |
Способ загрузки готовой смеси в автотранспорт |
гравитационный (два места загрузки - из-под смесителя или агрегата готовой смеси) |
Общая вместимость бункеров агрегата минерального порошка, м3 |
2 x 32,5 = 65 |
Общая вместимость цистерн для битума, м3 |
4 x 30 = 120 |
Тип пылеулавливающего устройства |
на выбор: рукавные фильтры или комбинированный: сухой (циклоны), мокрый (скруббер "Вентури") |
Способ утилизации пыли |
использование в техпроцессе |
Тип дозаторов |
весовые на тензодатчиках |
Система управления |
на выбор: релейно-контактная или микропроцессорная |
Привод исполнительных механизмов |
электропневматический |
Номинальное давление в пневмосистемах, МПа , (кгс/см2) |
0,6 (6) |
Габаритные размеры, м, длина / ширина / высота |
45/43,2/19 |
Модификации установки
Марка |
Наименование продукции |
ДС-168 |
для работы на жидком топливе с релейно-контактной системой управления |
ДС-1683 |
для работы на жидком топливе с микропроцессорной системой управления |
ДС-1686 |
для работы на природном газе с релейно-контактной системой управления |
ДС-16863 |
для работы на природном газе с микропроцессорной системой управления |
ДС-1687 |
для работы на жидком топливе с релейно-контактной системой управления и рукавными фильтрами |
ДС-16837 |
для работы на жидком топливе с микропроцессорной системой управления и рукавными фильтрами |
ДС-16867 |
для работы на природном газе с релейно-контактной системой управления и рукавными фильтрами |
ДС-168637 |
для работы на природном газе с микропроцессорной системой управления и рукавными фильтрами |
|
 |
 |
 |
|